The Expert's Corner
Scrapers Prove Essential for Efficient Heat Transfer
May 1, 2019
BACKGROUND
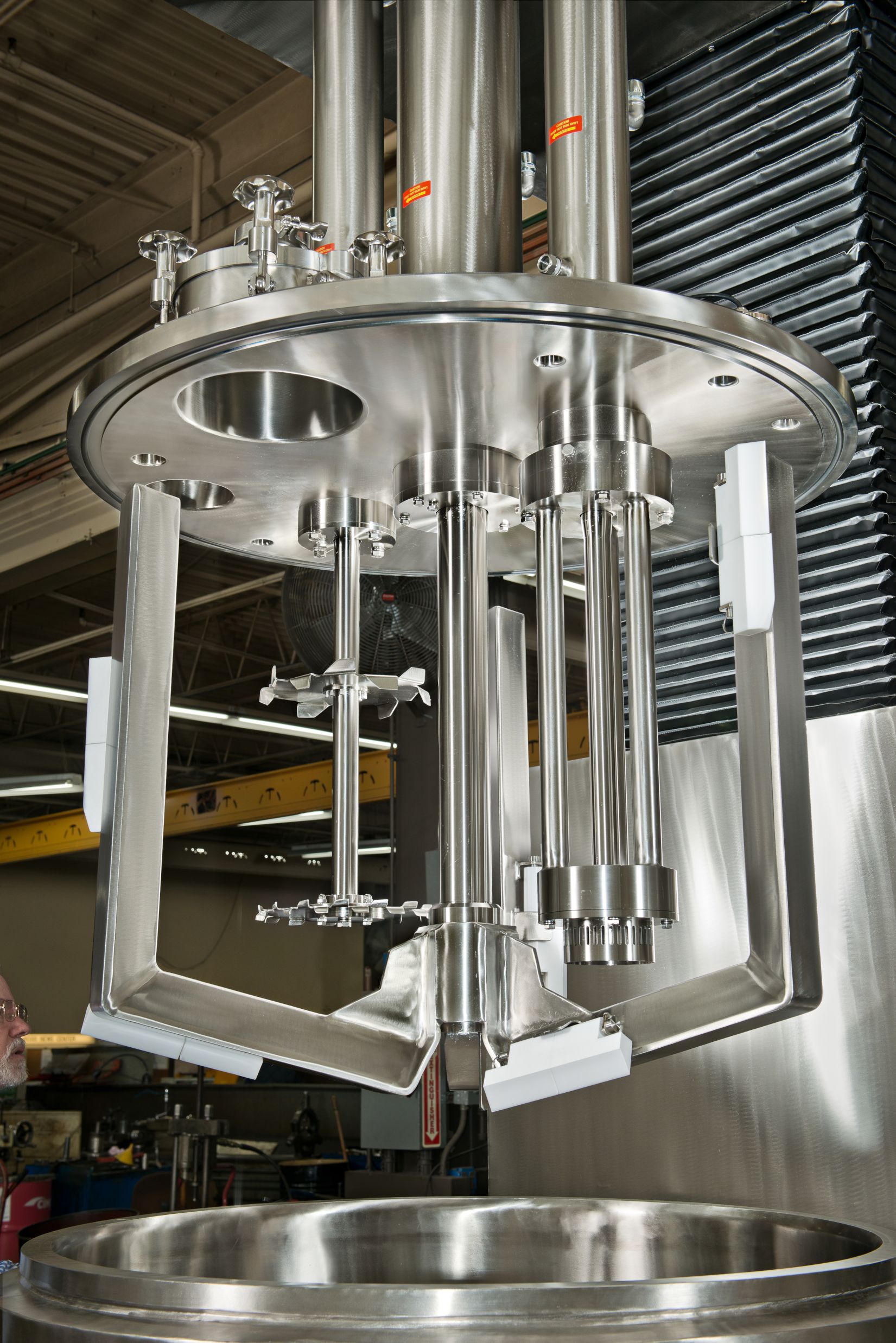
It is well accepted that scraping the inner surfaces of a process vessel will improve product homogeneity by removing materials from the walls and bottom and incorporating them into the bulk of the batch.
It is also a common practice to include wall and bottom scraping devices in the interest of improving heat transfer across the wall of a jacketed vessel.
In this technical brief we attempt to quantify the benefits of scraping the vessel walls of a Ross VersaMix. This is an important illustration as many emulsion based cosmetic creams and lotions require precise and responsive temperature control, especially in the cooling cycle, to effect the desired result.
EXPERIMENTAL
The mixer used in this experiment was a 100-gallon Ross VersaMix Model VMC-100. This VersaMix is equipped with an Anchor Agitator, a High Speed Disperser and a High Shear Mixer, however, for this demonstration, only the Anchor was used (most critical cooling cycles of emulsion based creams and lotions are performed with low shear agitation).
The VMC-100 was filled with 80 gallons of a 1% Carbopol 1342NF solution with a viscosity of approximately 20,000 cps. The Anchor was run at a constant speed of 20 rpm for the heating and cooling cycles of the test runs.
The heating and cooling source was a Mokon 12 kw water heat transfer system.
Temperature measurement was taken three ways: through a top-entering probe type thermocouple, a flush mounted thermocouple located in the bottom of the vessel, and a hand held digital thermocouple probe for verification of the other probes. Because the bottom thermocouple and the hand held probe were deemed most accurate, these readings were used for the data reduction.
This VMC-100 has a two-zone jacket, one for the side walls and the other for the bottom. Only the side wall jacket was utilized to avoid affecting the reading of the bottom entering thermocouple.
The first experiment entailed heating the batch from 80F to 2OOF, and then cooling back down to 80, with hinged Teflon scrapers on the Anchor. The second experiment was an exact repeat of experiment #1, with the exception that the scrapers were removed from the anchor.
OBSERVATIONS
It is obvious from the graph on the next page that having Teflon scrapers on the Anchor agitatorgreatly improved heat transfer from the jacket to the product. This was especially noticeable during the cooling cycle, an important factor as the cooling of emulsion based creams and lotions require efficient and rapid response to the desired temperature changes.
CONCLUSION
It can be determined from the results of the above experiment that the addition of wall and bottom scrapers is extremely important when processes require fast response to temperature changes.
It can be deduced from the data that by using scrapers, heating cycles are reduced by approximately 15% while cooling cycles can be reduced by approximately 60%. This disparity can be explained by the normal tendency of most materials to decrease in viscosity when heated, and to increase in viscosity when cooled. During the heating cycle, the jacket is hot, which drops the viscosity of the layer of product adhering to the walls in a non-scraped vessel. Since the viscosity is lowered by the heat, the layer tends to move off the wall easily, therefore, not creating a substantial insulating layer on the walls.
During the cooling cycle, the jacket is cool which increases the viscosity of the boundary layer on the wall, impeding the heat exchange between the jacket and the bulk of the product.
APPLICATIONS
In addition to applications in the cosmetics industry, the use of scrapers is applicable to any mixer in any industry requiring effective heat transfer between a vessel jacket and the product being mixed.